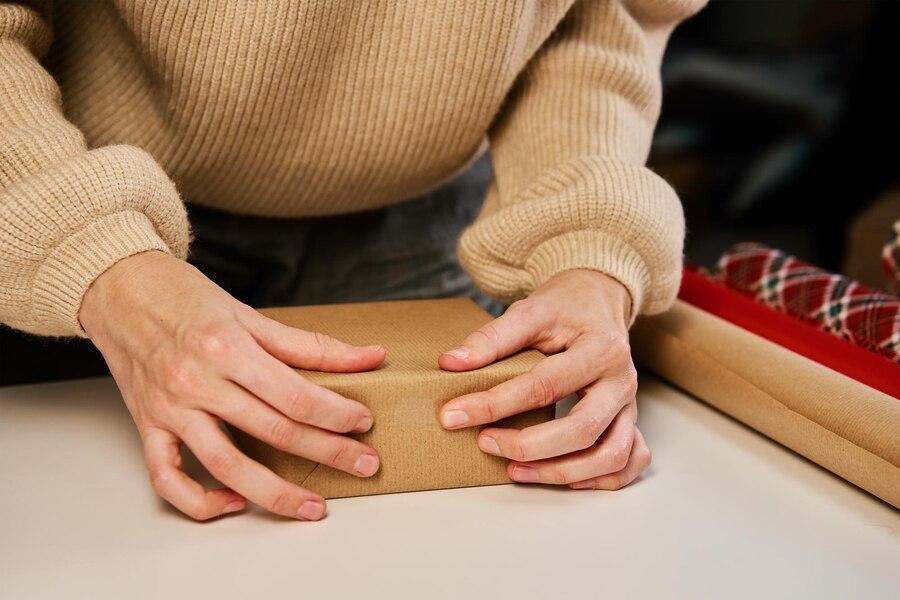
Nitrogen is delivered directly to the custom glove box. The antechamber is filled with nitrogen via the custom marine glove-box. Two valves connect the glove box technology and the antechamber, refilling (on the glove box’s external right wall) and evacuation (before the antechamber). The automated pressure control regulates the glove box refilling process. The upper line, with orange dots, indicates whether the glove box boxing is over- or under-pressure. Dots on the right indicate under pressure. Dots on the left indicate over-pressure. The lower line allows you to set the level of over-pressure/under-pressure using two red dots, each signifying the maximum or minimum. They can be moved by rotating the two little buttons.
Ventilated Antechamber For Glove-Packaging Boxes:
Inserting parts into the custom glove boxes while protecting the operator and the surroundings.
Stainless steel ventilated antechamber, Ø400mm lg600mm. The cubical ventilated antechamber with Ø250 door. Specially ventilated antechambers are available upon request, including cylindrical, cubic, and other materials. This equipment can be placed in the following glove box models. High-security isolator for neutral gas filtration in depression or over-pressure under filtered environment.
Clear Acrylic Custom Marine Glovebox with Antechamber:
In most circumstances, vacuuming the main chamber is unnecessary. The antechamber measures 9.5*9.5*9.5 inches (240*240*240mm) and is identical to those of MC variants. It can be vacuumed, thus pollution of the main chamber is greatly reduced. The acrylic thickness for the main chamber is 10mm. When compared to the vacuum custom glove manufacture box, using fewer acrylic materials saves a significant amount of money.
Acrylic glove box technology is suitable for usage in laboratories and clean rooms for chemical and biological research, pharmaceutical manufacturing, semiconductor manufacturing, and 3D printing.
Heated Antechamber Configuration of Glove Box Technology:
Press the Enter key three times. Press the Return key eight times. Press the UP arrow once until the screen reads “1”, then press Enter to confirm. This takes you to the first step settings. Press the Return key once. You are now on the temperature of the glove packaging adjustment screen. Press the return key to go to the time setting screen. Time is specified for custom marine glove boxes in minute and hour increments. To confirm your time interval, press the Enter key. Press the return key to go to the Step.
Environmental.Health and Safety of Custom Marine Glove Boxes:
Glove packaging boxes are sealed containers intended to protect the user, the process, or both by completely isolating the contents from the outside environment. They are normally outfitted with at least one set of gloves attached to the enclosure. The user manipulates the materials within with the gloves. A glove-manufacturing custom makeup box typically includes an antechamber for transferring goods into and out of the box.
Types of Custom Glove Boxes:
These provide oxygen and moisture-free conditions by replacing the air within the glove of custom makeup box technology with inert gas, such as nitrogen, argon, or helium, depending on the materials being worked with. A “rotary vane vacuum pump” is used to remove the atmosphere.
Conclusion:
Custom marine glove boxes provide an isolated working environment with minimal levels of oxygen and moisture. Most glove boxes will automatically expel inert gas via the system when contamination levels rise. To lower the amount of gas used and keep operating costs low, it is critical to limit atmospheric pollution as much as feasible. There are three primary sources of air contamination. Moisture and oxygen pass through the glove box walls, commonly known as ingress. Moisture and oxygen are released from the glove custom makeup box’s contents. Physical system leaks are produced by either damage or user fault.